Are Your Workers Trained to Use Permit to Work Systems
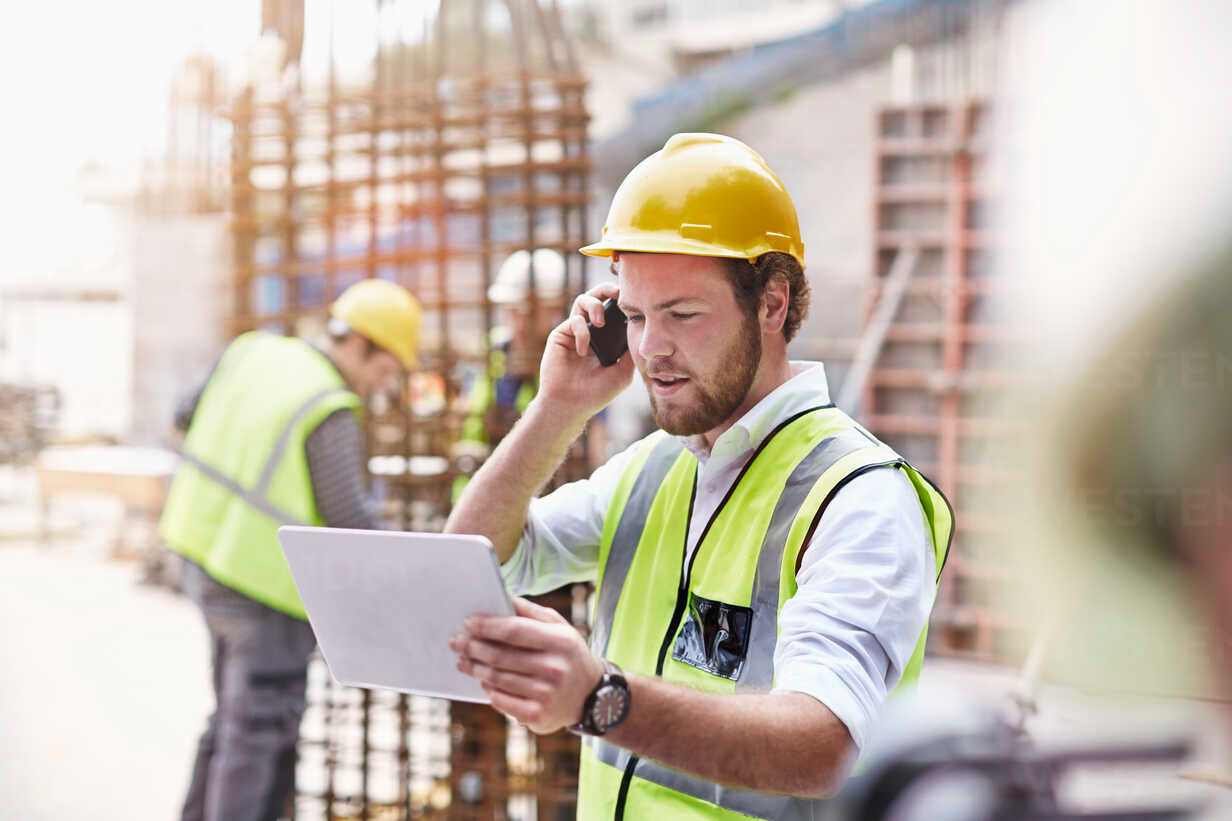
Are Your Workers Trained to Use Permit to Work Systems
A Permit to Work (PTW) system is a cornerstone of workplace safety, especially in high‑hazard environments such as oil & gas, chemical plants, or construction sites. However, no matter how well-designed the PTW system is, it only remains effective if workers understand and use it correctly. Poor training can cause misunderstandings, skipped steps, or even serious accidents.
Knowing the structure, scope, and content of these courses helps employers ensure their workforce is properly equipped to apply permit systems safely and confidently.
Why Training Matters
Even a clear permit form fails when users don’t understand its purpose or steps. Trained employees are more likely to:
- Fill permits accurately
- Recognize hazards
- Follow energy isolation steps like lockout/tagout
- Understand roles in issuing, receiving, and closing permits
Without proper training, permits become meaningless paperwork. Real-world stories confirm that small training gaps can lead to major incidents.
Many organizations seek professional development through Safety Officer Courses, which include comprehensive training on PTW systems, hazard awareness, and controllable behaviors.
Anecdote
On a maintenance site in Lahore, a worker restarted equipment during hot work, believing the permit had expired. He hadn’t been trained on how to interpret permit timings. The result? Sparks ignited nearby debris, causing a minor fire. This incident highlighted how a lack of training on permit use can easily turn into a hazard.
Step 1: Assess Current Competency Levels
Evaluate Permit Knowledge
Use simple quizzes or interviews to check if workers fully understand permit sections, hazard identification, and controls.
Observe Permit Use in the Field
Watch workers during permit-controlled tasks. Do they follow steps correctly? Do they ask questions if unsure?
Gather Feedback
Ask permit issuers, receivers, and supervisors where knowledge gaps exist or what confuses them most.
Step 2: Design Targeted Training Content
Cover Permit Basics
Teach essential permit types (hot work, electrical, confined space), legal requirements, and hazard controls.
Include Role Education
Clarify roles: who can issue, receive, approve, supervise, and close permits—along with responsibilities.
Emphasize Critical Content
Explain energy isolation (like lockout/tagout), permit timing, revalidation, and handover procedures.
Step 3: Use Engaging Training Methods
Combine Theory with Practice
Include hands-on exercises like filling dummy permits and walking through work zones.
Use Role‑Play and Scenarios
Simulate real situations—such as issuing permit under time pressure or handling shift handovers—that encourage discussion and recall.
Include Visual Aids
Use flowcharts, hazard maps, and PPE posters to reinforce learning.
Step 4: Reinforce Learning on Site
Tool‑box Talks Redirect Learning
Discuss PTW topics in daily briefings: permit errors seen last week, unusual incidents, or refresher steps.
Mentorship of New Staff
Seasoned workers or supervisors should mentor new hires on real permit use and pitfalls.
Participant-Driven Feedback
Encourage learners to identify confusing steps and co-develop solutions.
Step 5: Evaluate Training Impact
Observe Post-Training Permit Execution
Track whether documentation errors drop and compliance increases.
Use Regular Quizzes or Refreshers
Occasionally test staff knowledge to reinforce retention and highlight knowledge gaps.
Review Incident or Near-Miss Trends
Check if permit-related near misses, handover mistakes, or isolation failures decline over time.
Step 6: Train Across All Roles
Permit Issuers and Approvers
Ensure they are competent in hazard identification and understanding permit workflows.
Permit Receivers and Workers
Train them on hazard awareness, permit validity, PPE use, and reading permit conditions.
Supervisors and Safety Teams
These groups must audit procedures, coach on permit mistakes, and reinforce proper behavior.
Step 7: Integrate Training into Safety Systems
Embed Permit Training in Safety Induction
Ensure new joiners receive PTW training before starting any hot work or high-risk tasks.
Refresh Training Regularly
Conduct formal training every 6–12 months or after incidents to maintain awareness.
Link Training with Technical Systems
Where digital PTW tools are used, include system navigation and error‑prevention training.
Step 8: Foster Continuous Improvement Culture
Encourage Worker Engagement
Invite teams to suggest improvements to permit forms, process flow, or training gaps.
Use Real Incident Debriefs
Discuss permit failures in safety meetings to reinforce learning and drive changes.
Promote Open Communication
Create safe channels for workers to raise concerns if they fear stepping in without repercussion.
Step 9: Audit Training Effectiveness
Conduct Role-Based Observational Audits
Assess how well trained staff perform permit activities in real settings.
Use Permit Error Tracking
Record mistakes such as missing fields, wrong isolation steps, or unreadable signatures and act on them.
Feedback Loop for Training Updates
Use audit results and participant input to adjust course content or delivery methods.
Step 10: Align Training with Professional Certification
Invest in Recognized Programs
Courses like NEBOSH or equivalent Safety Officer Courses include structured modules on PTW systems, hazard identification, and compliance best practices.
Focus on Practical Outcomes
Choose programs that include simulated permit writing, real case studies, and site-based scenarios.
Support Continued Development
Encourage employees to pursue advanced certifications that deepen their ability to audit, train, and lead PTW implementation.
Read more about Safety Courses to find training paths that empower your team with the skills needed to use Permit to Work systems effectively and build safer operations.
Conclusion
Training is the foundation of a functioning Permit to Work system. Workers need clear knowledge, real-world practice, and ongoing support to use it effectively. When structured training, observation, and professional development come together, permit systems become a living safety tool—not just paperwork. By investing in learning, mentoring, and strong systems, organizations build trust in safety processes and ensure workers feel confident every time they apply a permit.
If you’d like help designing training programs, creating audit tools, or building observer-feedback processes based on this guide, I’d be happy to assist.
- Art
- Causes
- Crafts
- Dance
- Drinks
- Film
- Fitness
- Food
- Juegos
- Gardening
- Health
- Home
- Literature
- Music
- Networking
- Other
- Party
- Religion
- Shopping
- Sports
- Theater
- Wellness
- Script
- App