Diamond Wafering Blade: The Ultimate Cutting Solution
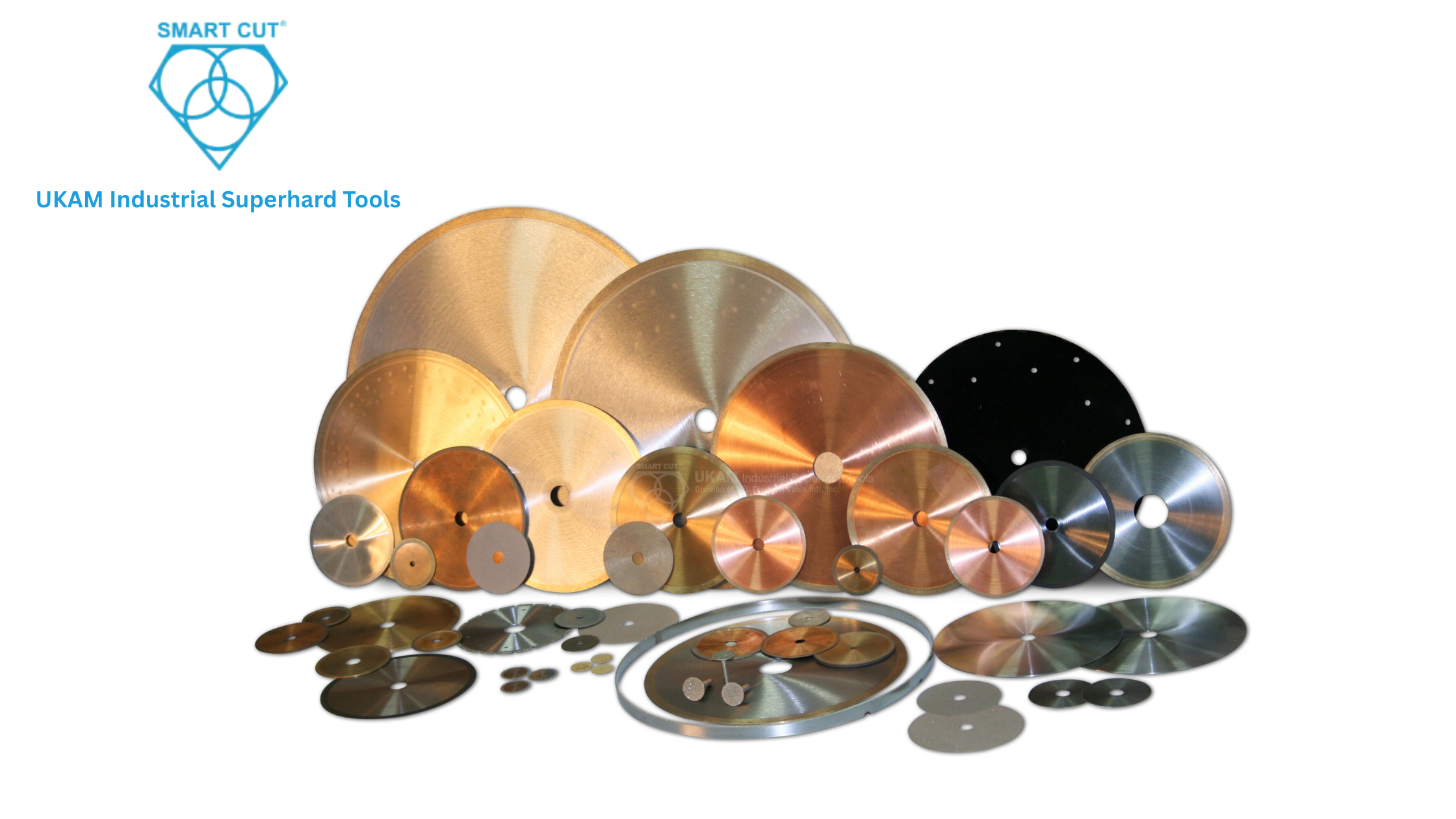
My colleague Jake nearly had a heart attack last week. He was cutting silicon wafers for a critical project when his regular blade chipped the entire batch. That's when I introduced him to the diamond wafering blade – and honestly, it saved his job. These tools aren't just another cutting implement; they're game-changers for anyone serious about precision work.
After fifteen years in manufacturing, I've seen countless cutting tools come and go. But diamond wafering blades? They've stuck around because they work—no gimmicks, no empty promises – just reliable performance when you need it most.
Why Diamond Wafering Blades Beat Everything Else
Look, I'm not here to sugarcoat things. Most cutting tools are mediocre at best. They promise precision but deliver headaches. Diamond wafering blades are different. They deliver on their promises.
The difference starts with the diamonds themselves. We're talking synthetic diamonds here – not the flashy jewelry kind, but industrial-grade particles that mean business. These diamonds get embedded into carefully engineered bond systems that hold them exactly where they need to be.
Here's what most people don't understand: it's not just about having diamonds on your blade. It's about having the RIGHT diamonds in the RIGHT places with the RIGHT bond. That's where the real magic happens.
Construction That Makes Sense
The blade core isn't some random piece of metal. Engineers spend serious time figuring out the perfect substrate material. Stainless steel works great for most jobs, but sometimes you need specialized alloys. The thickness varies wildly too, from paper-thin 0.1mm blades for ultra-precise work to beefier 2mm+ options for heavy-duty cutting.
Bond systems make or break these blades. Resin bonds work beautifully when you need smooth finishes. Metal bonds last forever, but cut more aggressively. Electroplated bonds? They're the bulldozers of the diamond world – use them when nothing else works.
Real-World Applications (Where These Blades Shine)
Semiconductor Manufacturing
Silicon wafer processing is unforgiving. One bad cut costs thousands. I've watched entire production runs get scrapped because someone used the wrong blade. Diamond wafering blades eliminate that risk. They cut clean, they cut precisely, and they don't leave you sweating about dimensional accuracy.
The semiconductor guys I work with swear by these blades. They've cut their reject rates in half just by switching from conventional abrasives.
Electronics Production
PCB manufacturing throws curveballs constantly. You're cutting through copper, fiberglass, ceramics – sometimes all in the same cut. Regular blades struggle with material transitions. Diamond wafering blades handle these mixed-material challenges without breaking stride.
One electronics manufacturer I consulted for increased their yield by 23% after switching to diamond blades. The improved cut quality eliminated downstream defects that were costing them serious money.
Research and Development
Lab work demands perfection. When you're analyzing material properties or studying failure modes, the cutting process can't introduce artifacts. Diamond wafering blades provide clean, undisturbed cross-sections that reveal true material characteristics.
Research labs particularly appreciate how these blades maintain consistent performance across different materials—no more adjusting parameters for every new sample type.
Automotive and Aerospace Industries
Modern vehicles and aircraft use exotic materials that laugh at conventional cutting tools. Carbon fiber composites, advanced ceramics, and titanium alloys – these materials require specialized approaches. Diamond wafering blades rise to these challenges consistently.
An aerospace supplier I worked with reduced their machining time by 40% after implementing diamond blade technology. The improved efficiency translated directly to their bottom line.
Selecting the Right Blade (It's Not Rocket Science)
Choosing blades doesn't require a PhD, but it does require understanding your specific needs. Material hardness matters tremendously. Soft materials need harder bonds to prevent loading. Hard materials require more aggressive cutting action.
Diamond grit size creates interesting trade-offs. Fine grits produce mirror finishes but cut more slowly. Coarse grits rip through materials quickly but leave rougher surfaces. Most applications fall somewhere in the middle.
Bond concentration affects both performance and economics. Higher concentrations last longer but cost more initially. Lower concentrations cut faster but need frequent replacement. Smart buyers calculate the total cost of ownership, not just the purchase price.
Working with Professional Manufacturers
Partnering with an experienced diamond tools manufacturer changes everything. These aren't just vendors selling products – they're problem-solving partners who understand your challenges.
Custom blade development opens doors that most people don't even know exist—working with experimental materials? Pushing precision boundaries? Skilled manufacturers engineer solutions that standard catalogs can't touch.
The technical support alone justifies these partnerships. When you're stuck with a challenging application, having experts to call makes all the difference.
Operating Tips That Work
Proper operation separates successful users from frustrated ones. Spindle speed selection requires balancing efficiency with heat generation. Too fast burns everything. Too slow kills productivity. Finding the sweet spot takes experimentation.
Feed rates need careful attention. Aggressive feeding overloads blades, causing premature failure. Conservative feeding glazes diamond particles, reducing effectiveness. The optimal balance depends on your specific application.
Cooling systems aren't optional – they're essential. Adequate coolant flow removes heat and debris, keeping diamonds sharp and effective. Water-based coolants work well for most jobs, though some materials require specialized fluids.
Maintenance That Extends Blade Life
Proper maintenance dramatically extends blade life. Regular cleaning removes debris that interferes with the cutting action. Use appropriate solvents and gentle techniques to avoid damaging the diamond matrix.
Storage practices matter more than most realize. Protective cases prevent edge damage and contamination. Climate-controlled storage prevents corrosion and maintains bond integrity. These simple steps often double the blade life.
Complementary Cutting Technologies
Diamond wafering blades work exceptionally well with diamond dicing blades for comprehensive cutting solutions. While wafering blades excel at precision sectioning, dicing blades handle different cutting patterns and geometries.
Understanding how these technologies complement each other helps manufacturers develop integrated strategies. The combination provides flexibility that single-tool approaches simply cannot match.
Quality Control Strategies
Consistent performance requires systematic quality control. Regular inspection protocols catch problems before they impact production. Visual checks, dimensional measurements, and performance testing all contribute to reliable operations.
Performance validation confirms blade suitability for specific applications. Test cuts on representative materials provide crucial data about cutting forces, surface quality, and expected tool life. This information guides both selection and optimization decisions.
Industry Trends and Future Developments
The diamond blade industry evolves rapidly. Advances in synthetic diamond technology produce harder, more uniform particles. New bond systems offer improved performance characteristics. Manufacturing processes become more precise and consistent.
Automation integration represents a significant trend. Automated systems demand blades with predictable performance and consistent wear patterns. This drives development toward more standardized, reliable products.
Frequently Asked Questions
What materials cut best with diamond wafering blades?
Silicon, ceramics, glass, composites, and various metals all respond well to properly selected diamond blades.
How thin can these blades get?
Current technology allows blades as thin as 0.1mm for applications requiring minimal material loss.
What factors determine blade life?
Material properties, cutting parameters, cooling effectiveness, and handling practices all significantly impact longevity.
Can worn blades be resharpened effectively?
Most diamond wafering blades cannot be resharpened due to their thin profile and specialized construction.
Which cooling methods provide the best results?
Water-based coolants typically offer optimal heat removal and debris flushing for most applications.
How should I choose diamond particle size? Consider the trade-off between surface finish quality (finer particles) and cutting speed (coarser particles).
What causes premature blade failure?
Excessive speeds, inadequate cooling, improper feed rates, and contamination are primary failure causes.
Are custom blades readily available?
Yes, experienced manufacturers offer custom development services for unique requirements and challenging applications.
Diamond wafering blades represent a mature technology that continues delivering exceptional results across multiple industries. Their combination of precision, durability, and versatility makes them indispensable tools for manufacturers who refuse to compromise on quality. Whether processing semiconductor wafers or sectioning advanced composites, these cutting tools consistently deliver the performance modern manufacturing demands.
The investment in quality diamond wafering blades pays dividends through improved yield rates, reduced processing time, and enhanced product quality. Smart manufacturers recognize that cutting tool selection directly impacts their bottom line, and diamond wafering blades deliver measurable returns on investment.
- Art
- Causes
- Crafts
- Dance
- Drinks
- Film
- Fitness
- Food
- Spiele
- Gardening
- Health
- Home
- Literature
- Music
- Networking
- Other
- Party
- Religion
- Shopping
- Sports
- Theater
- Wellness
- Script
- App